Empresa brasileira usa cogumelo como cola natural para criar material sustentável
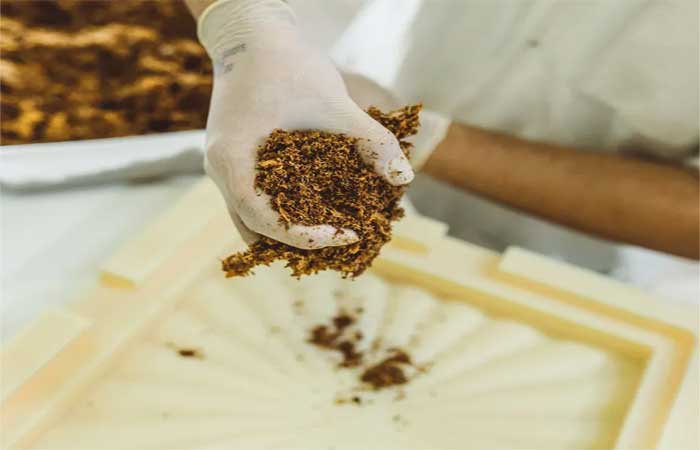
Negócio começou na universidade e, segundo fundador, não gera lixo nem emite CO2
Fundada em Ponta Grossa, no Paraná, a Mush propõe uma forma diferente de utilizar os cogumelos para criar soluções sustentáveis. A empresa usa os fungos como uma cola natural para juntar resíduos agrícolas, gerando um material biodegradável que pode ser moldado em diferentes formatos. O negócio hoje emprega a inovação nas áreas de arquitetura e design e já recebeu cerca de R$ 2,5 milhões em investimentos.
A Mush foi criada em 2019 por Eduardo Sydney, Leandro Oshiro e Antonio Carlos de Francisco. O negócio começou dentro da Universidade Tecnológica Federal do Paraná e tinha como proposta inicial a produção de embalagens sustentáveis a partir de fungos. O modelo, porém, requer uma escala de produção muito grande, que não seria viável dentro do laboratório da universidade. Após uma pesquisa de mercado, os sócios decidiram pivotar.
“Buscamos novos produtos, utilizando a mesma tecnologia, que contribuíssem ambientalmente no tratamento de resíduos e melhorassem a qualidade de vida das pessoas dentro dos ambientes fechados”, diz. O primeiro resultado foi a criação de produtos de revestimento acústico, que ajudam a evitar o eco.
Com o lançamento dessa solução, em 2021, eles conseguiram um investimento de R$ 300 mil da aceleradora Ventiur. Os recursos ajudaram a aumentar a escala de produção, em um formato piloto. No final daquele ano, a Mush estava com uma fábrica estabelecida e operante.
Em 2022, foi o momento de se concentrar na parte comercial. “Fizemos a inserção desse tipo de material no mercado, apresentação em eventos, exposições, principalmente no setor de arquitetura”, diz Sydney. Ao longo do ano, a empresa captou mais R$ 1,2 milhão com investidores-anjo.
Agora, a Mush negocia um investimento R$ 1 milhão com um fundo de Corporate Venture Capital (CVC). O plano é aumentar em dez vezes a capacidade de produção.
/i.s3.glbimg.com/v1/AUTH_7d5b9b5029304d27b7ef8a7f28b4d70f/internal_photos/bs/2023/j/h/9vq0iUSZ6FmzNVAUpVOw/colecao-cosmos-primeira-criada-pela-mush-com-itens-de-decor-para-ambientes-infantis-com-pigmentos-naturais-que-brilham-no-escuro-.jpg)
A Mush já produziu uma variedade de produtos feitos a partir do material, incluindo itens decorativos insfantis com pigmentos naturais que brilham no escuro — Foto: Divulgação/Mush
Entre cogumelos e resíduos agrícolas
Os resíduos agrícolas são a matéria-prima principal da empresa. Entre eles estão palhas, cascas, bagaços e serragem. “Esses materiais são os que geralmente sobram da produção tanto de alimentos quanto de madeira”, aponta o engenheiro.
O resíduos são utilizados como fonte de nutrientes para os fungos. O micélio, parte vegetativa do cogumelo, é usado como cola natural, que se agrega ao substrato, formando um novo material.
O processo é feito dentro de moldes, o que faz com que o produto final possa adquirir o formato desejado. “Ao final, esse fungo é inativado, então ele não está mais vivo. O material se torna estável e dura para sempre”, explica.
O produto final é orgânico e biodegradável, podendo ser usado como fertilizante de plantas. Segundo Sydney, essa cadeia de produção não emite gás carbônico e nem gera lixo. “Estamos traçando um caminho para nos tornarmos carbono negativo e gerar crédito de carbono”, complementa.
Recentemente, o material teve a patente depositada pelo Instituto Nacional da Propriedade Industrial (INPI). “Nós somos os primeiros na América Latina a produzir e comercializar materiais utilizando micélio e agora estamos entrando com o pedido mundial”, conta o fundador. “Ficamos felizes de mostrar que podemos gerar novas soluções com o impacto socioambiental positivo dentro das universidades públicas.”
Produtos e escala de produção
Além do revestimento acústico, a Mush desenvolve artigos de decoração em parceria com escritórios de design. Pelo fato de o material ser produzido dentro de um molde, a empresa também cria itens exclusivos para os clientes, que podem ser pessoas físicas ou empresas.
“Nesse nosso primeiro ano, fizemos revestimento acústico, luminária, obra de arte, quadros que as pessoas pintam e até uma urna mortuária”, exemplifica Sydney. Em formato de um pequeno barco, a urna produzida pode se degradar no mar.
/i.s3.glbimg.com/v1/AUTH_7d5b9b5029304d27b7ef8a7f28b4d70f/internal_photos/bs/2023/u/8/Q7ZTVXTnSu3C6rwJop6w/mesa-sertao-primeiro-movel-a-base-de-cogumelos-no-pais-collab-mush-e-anima-studio-design-foto-divulgacao.jpg)
Mesa Sertão, resultado da collab entre Mush e Anima Studio Design — Foto: Divulgação/Mush
As soluções são precificadas por quilo do material. Sydney não revela o valor, alegando que ele ainda pode sofrer alterações. Porém, diz esperar atingir um preço competitivo com o isopor. “Na minha escala piloto, 70% do meu custo é mão de obra. Agora eu começo a mecanizar e automatizar processo”, diz.
O engenheiro acredita que só vai conseguir causar impacto social e ambiental quando a solução for acessível para todos. Por isso, a redução de custos de operação é um dos principais focos para 2023. Além disso, com o aumento da escala de produção, a Mush pretende voltar para a área de produção de embalagens, visando expandir a sua atuação na construção civil.